Profilowanie ploterów wielkoformatowych (cz. 2)
Z lektury pierwszej części artykułu wiemy już, jakie kolory chcielibyśmy osiągnąć w druku (zgodne z normą FOGRA39) i widzimy je na proofie. Mamy ploter ink-jetowy drukujący w jakiejś technologii (UV, latex, solvent, pigment, itp.). Mamy też podłoże do druku (papier, folia, hips, plexi, dibond, itp.). Mamy także program do druku, tzw. RIP (Raster Image Processor), który przelicza plik przeznaczony do druku i wysyła dane do plotera. Drukujemy naszą pracę i okazuje się, że kolory mocno różnią się od tych na proofie. Co robić?
Musimy pamiętać o tym, że zarządzanie kolorem działa poprawnie tylko wtedy, gdy wszystkie jego ogniwa są sprawne i dobrze połączone. Czyli gdy mamy prawidłowo ustawione wszystkie opcje w RIP-ie (a jest ich niemało) oraz mamy wykonane dedykowane profile dla każdego podłoża. Bez tego, szukając satysfakcjonującego nas koloru w druku, jesteśmy zdani na przypadkowe przestawianie różnych opcji w nadziei, że w końcu wydruk wyjdzie prawidłowo. Zazwyczaj mijają godziny, tusz i podłoże się marnują, a frustracja rośnie. Same straty.
Zarządzanie kolorem działa poprawnie tylko wtedy, gdy wszystkie jego ogniwa są sprawne i dobrze połączone.
Po co tworzyć profil podłoża?
Po pierwsze dlatego, aby uzyskać prawidłowe kolory. Ale tworzenie profilu ma głęboki sens także z innych powodów. Pozwala oszczędzić tusz, czasami wręcz w stopniu zdumiewającym. Pozwala także rozpoznać prawdziwe możliwości plotera, co może mieć ogromne znaczenie przy drukowaniu kolorów dodatkowych zdefiniowanych w pliku (np. kolorów Pantone). Jeśli tusze i podłoże pozwalają na wydruk większego gamutu (bardziej nasyconych kolorów) niż standardowy CMYK, to dobry RIP będzie potrafił to wykorzystać! W profilu znajdą się też informacje o bieli podłoża oraz o najciemniejszych kolorach, gdzie bardzo istotny jest parametr sumy tuszy, które można wylać w jednym miejscu, aby uniknąć niedoschniętych wydruków, zalanych szczegółów itp., ale przy tym uzyskać możliwie głęboką i neutralną czerń.
Jak się tworzy profil podłoża?
Do stworzenia profilu podłoża potrzebne jest odpowiednie oprogramowanie. Najczęściej jest to dodatkowy moduł programu RIP (Raster Image Processor). Konieczny jest także spektrofotometr, czyli urządzenie odczytujące kolor z wydruku (np. X-Rite i1 Pro 2). Oczywiście musimy też mieć sprawny ploter oraz podłoże do druku. Bardzo ważne jest wyczyszczenie głowic przed profilowaniem. Jeśli zrobimy profil z użyciem głowic, które mają zatkane dysze to potem po ich wyczyszczeniu kolor się zmieni, a profil trzeba będzie tworzyć od nowa.
Generalnie proces tworzenia profilu polega na wydrukowaniu serii testów złożonych z pewnej ilości prostokątnych pól pomiarowych. Każdy taki wydruk podlega pomiarom, dzięki którym program dowiaduje się jak dany kolor wychodzi w druku. Oprócz pomiarów, część wydruków testowych podlega ocenie okiem.
Poniżej omówię w skrócie, jak przebiega przykładowe profilowanie plotera korzystającego tylko z czterech tuszy CMYK, bez kolorów „light” oraz innych tuszy dodatkowych. To najprostszy przypadek, ale wystarczy do zrozumienia samego procesu. Plotery z większą ilością tuszy profiluje się nieco inaczej, w pewnych przypadkach tworzy się także dla ploterów profile RGB, co ma duży sens.
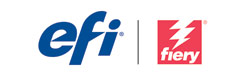
EFI Fiery XF
To bardzo uniwersalny i bardzo funkcjonalny RIP. Obsługuje ponad 750 ploterów drukujących, pozwala tworzyć własne profile i certyfikować proofy.
Krok 1 – Limit tuszu
Większość ploterów domyślnie przelewa tusz. To znaczy, że zużywa go więcej niż potrzeba. Spotkałem nawet takie egzemplarze, które drukują pełną aplę już dla 50% wartości koloru w pliku, czyli wszystko co w pliku miało od 50% do 100% drukowane było jak pełna apla 100%. To jest oczywiście koszmar, ponieważ wydruki są za ciemne, szczegóły w ciemniejszych miejscach pozalewane, tusz marnuje się, a do tego pojawiają się problemy ze schnięciem.
Pierwszym krokiem jest więc wydrukowanie kratek z przyrastającą wartością dla każdego kanału tuszu i sprawdzenie czy dany kanał przelewa, a jeśli tak, to przy jakiej wartości procentowej.
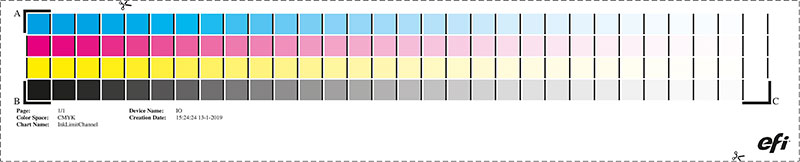
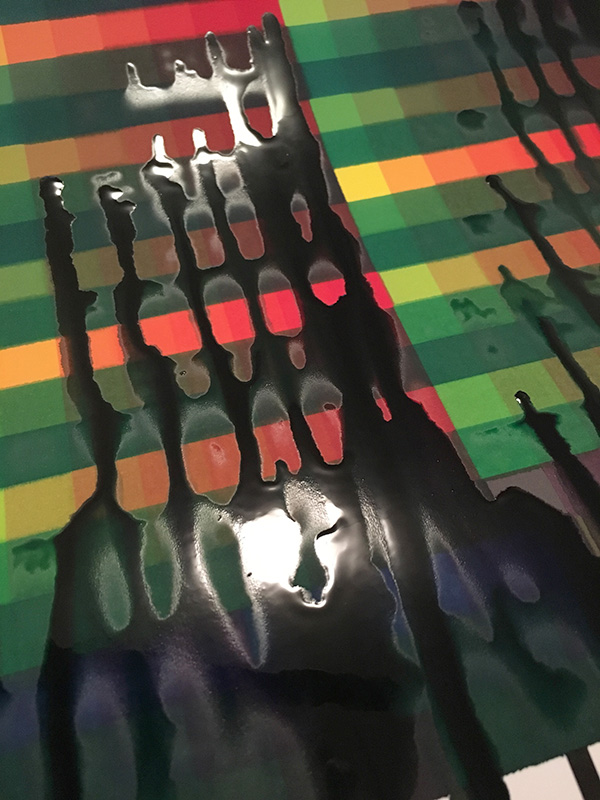
Niewiarygodny, ale niestety prawdziwy przykład przelewania. Tusz płynie w sensie dosłownym.
Krok 2 – Linearyzacja
Proces linearyzacji kanałów polega na tym, aby sprowadzić każdy kanał tuszu do pracy liniowej. To znaczy jeśli w pliku jest np. 50% magenty, to na wydruku także powinno być 50% magenty. Analogicznie mają się zachować wszystkie inne wartości. Jest rzeczą powszechną, że kanały w ploterach nie są liniowe i najczęściej przelewają. Na przykład tam, gdzie w pliku mamy wartość 50%, na wydruku wychodzi 60%.
Wydruk do linearyzacji wygląda podobnie jak do limitu tuszu, ale posiada istotną różnicę. Tutaj pełna apla (czyli 100% w kanale tuszu) jest już ograniczona do wartości wcześniej ustalonego limitu tuszu. Czyli przykładowo, jeśli cyan przelewał już od 70%, to kratki do linearyzacji (i wszystkie późniejsze wydruki) będą już wypuszczane tylko w zakresie 0% – 70%.
Po zmierzeniu kratki linearyzacji, program już wie, jaka jest nieliniowość każdego kanału i może ją skorygować w czasie obrabiania danych do druku. Trzy wykresy poniżej prezentują korektę sumy kolorów oraz linearyzacji dla trzech różnych modeli ploterów. Wykresy pochodzą z pomiarów prawdziwych urządzeń.
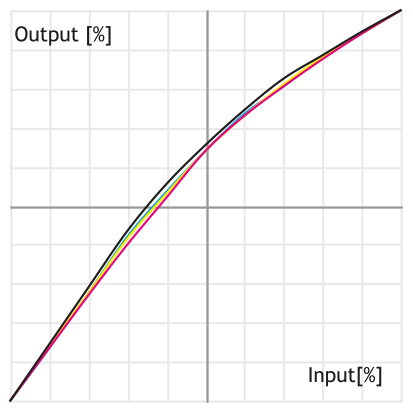
Ploter dobry
Nie było potrzeby ograniczania tuszu w kanałach. Należało tylko przywrócić liniowość, ponieważ ploter drukował trochę za jasno.
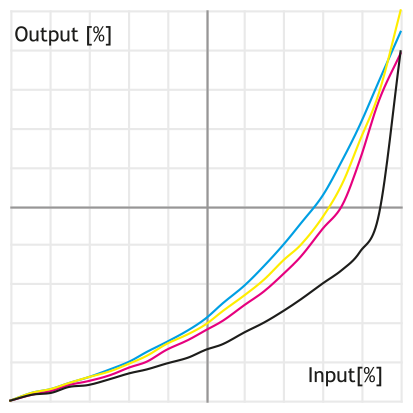
Ploter średni
Wystarczyło niewielkie ograniczenie tuszy. Ale konieczna była znaczna poprawa linearyzacji, ponieważ ploter mocno przelewał kolory, szczególnie czarny.
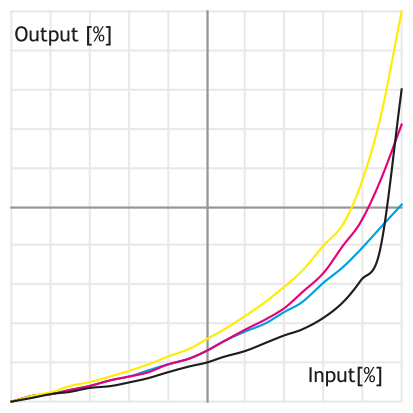
Ploter zły
Należało poprawić ogromne przelewanie tuszu oraz skorygować bardzo duże nieliniowości.
Krok 3 – Suma kolorów
W druku offsetowym każdy papier potrafi przyjąć pewną ilość farby (np. 330%), a gdy jest jej za dużo to są problemy ze schnięciem, przesiąkaniem itp. Podobnie w ploterach, gdy nadrukujemy w jednym miejscu za dużo tuszu, to pojawiają się kłopoty. Druk solventowy potrafi długo schnąć, pigmentowy się rozmazuje albo uzyskuje matowy nalot. Druk UV jest raczej odporny ze względu na natychmiastowe utwardzanie promieniami UV, ale można tak nieszczęśliwie dobrać parametry druku, że też nie wyschnie. Krótko mówiąc trzeba poszukać takiej ilości tuszu, która będzie satysfakcjonująco szybko schła. Ale nie możemy ograniczyć go nadmiernie, ponieważ wtedy głębokie czernie zaczną wychodzić blado. Musimy znaleźć złoty środek.
Krata testowa dla sumy kolorów powinna zawierać część pomiarową i część do oceny optycznej. W zależności od technologii druku, czasem lepiej jest skorzystać z pomiarów, a czasem ocenić „na oko”. Przykładowo druk pigmentowy, który zazwyczaj dobrze schnie, lepiej jest pomierzyć. Natomiast druk solventowy, który często nadcieka, trzeba koniecznie oceniać także optycznie. Dla odmiany druk UV dobrze jest pomacać, bo ograniczenie ilości tuszu tutaj często wręcz da się wyczuć pod opuszkiem palca.
W tym kroku decydujemy (wspomagając się pomiarami) ile maksymalnie tuszu będzie wylewane na podłoże. Czasem to jest 350%, czasem musimy zejść aż do 240% a dla kapryśnych podłoży, bywa, że jeszcze mniej.
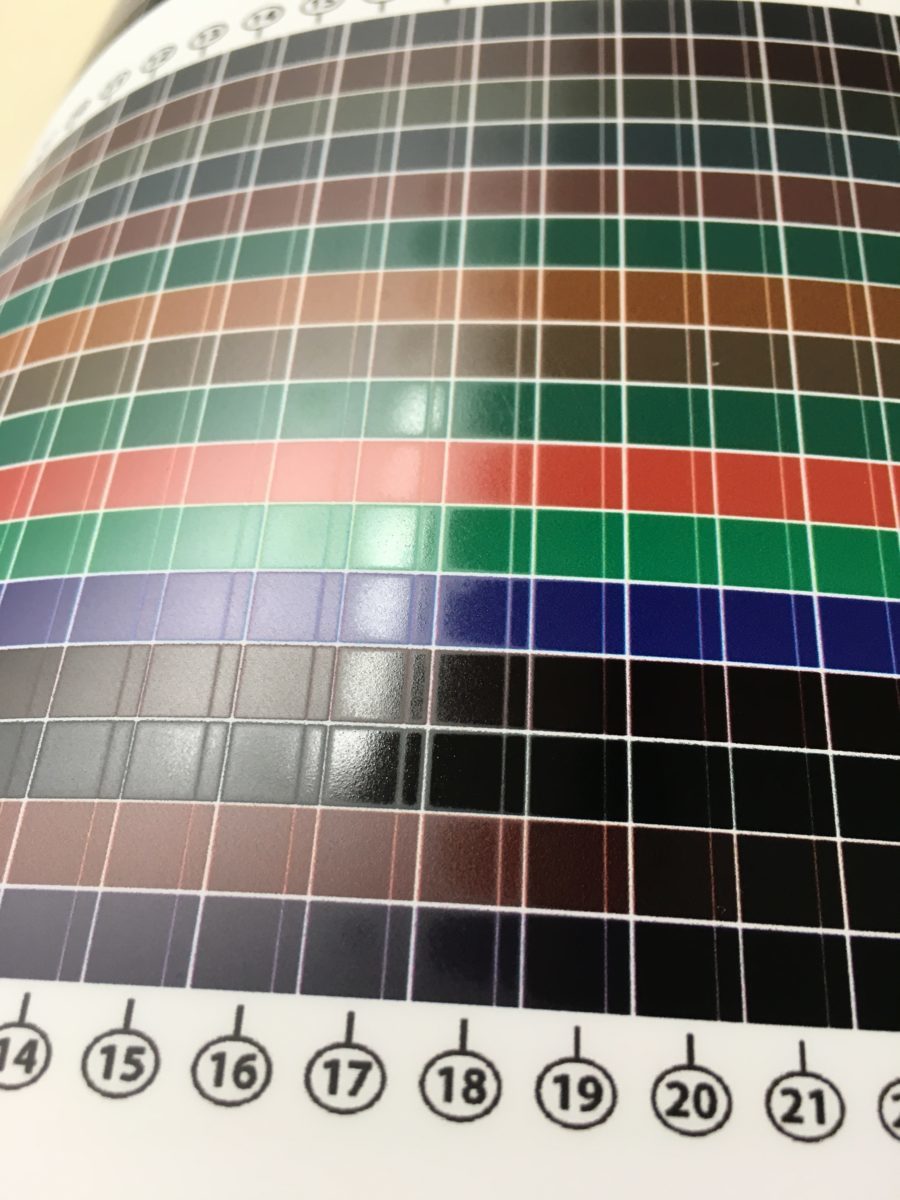
Na zdjęciu widać obszary niedoschnięte, które się błyszczą.
Krok 4 – Neutralizacja szarości
Wbrew pozorom, najważniejsze kolory w druku to kolory szare, a nie te nasycone. Najpiękniejszy wydruk może zostać zepsuty, jeśli szarości nie będą neutralne. Oko ludzkie jest w tym zakresie bardzo czułe, z łatwością dostrzegamy nawet drobne zabarwienia szarości. Jeśli ktoś drukował zdjęcia czarno-białe ze składowych CMYK, to wie w czym rzecz. Dlatego w przypadku profilowania mediów, dla niektórych ploterów wykonuje się dodatkowy krok, którego celem jest właśnie neutralizacja szarości.
Drukowany test, to zestaw pól, które są szare oraz mają niewielkie zabarwienia w różne strony. Oprogramowanie mierzy wartości dE, o jaką szare pola różnią się od idealnie neutralnej szarości a następnie to koryguje. Ten test ma charakter iteracyjny. To znaczy, że program po zmierzeniu pierwszego testu dostraja wartości i drukuje go ponownie. Mierzymy i obserwujemy, jak średnia dE spada, czyli szarość się neutralizuje. I tak możemy zrobić jeszcze kilka razy, aż osiągniemy bardzo niską wartość dE.
W praktyce spotkałem plotery, gdzie udało się w tym kroku zejść ze średnią dE z początkowych 6 do około 1,5. Efekt wizualny był bardzo łatwo zauważalny. Zatem zdecydowanie warto poświęcić trochę czasu na te czynności.
Krok 5 – Profil koloru
Na tym etapie mamy ploter z ograniczonymi i zlinearyzowanymi kanałami tuszy. Wiemy też do jakiej maksymalnej wartości możemy sumować tusze oraz dostroiliśmy szarości tak, aby były możliwie najbardziej neutralne. Posługując się analogią muzyczną, możemy powiedzieć, że wykonaliśmy „strojenie” plotera, a teraz czas na nim „zagrać” i zobaczyć jak brzmi, czyli jak drukuje.
Musimy teraz wykonać profil ICC, czyli sprawdzić, jak kolory wychodzą w druku z różnych mieszanek składowych CMYK. W tym celu należy wydrukować odpowiednio przygotowaną kratkę kolorów i je pomierzyć. Skoro podstawowym profilem, którego będziemy używać w druku jest FOGRA39, dobrze jest oprzeć się na tej specyfikacji i wydrukować takie same pola, które posłużyły do stworzenia tej normy. Wzorzec taki nazywa się IT8.7/4 i zawiera 1617 pól pomiarowych. Był przedstawiony w pierwszej części tego artykułu.
Po zmierzeniu wszystkich pól, profil zapisywany jest w pliku z rozszerzeniem ICC. Dopiero w tym momencie RIP ma pełną wiedzę na temat możliwości kolorystycznych danego plotera na konkretnym podłożu i może zacząć z tego korzystać. Jednak zanim zaczniemy drukować, warto przyjrzeć się samemu profilowi, ponieważ można z niego wiele wyczytać. O tym napiszę w trzeciej części artykułu.